Acrylic, a versatile and widely used material, has become a staple in industries ranging from construction to art and design. Known for its clarity, durability, and lightweight nature, acrylic serves as an excellent alternative to glass while offering unique properties that make it suitable for countless applications. But how does this remarkable material come to life? The journey of acrylic manufacturing—from raw materials to the polished sheets, rods, or molded products we encounter daily—is a fascinating blend of chemistry, engineering, and precision. Let’s explore this process step by step.
The Starting Point: Raw Materials
The creation of acrylic begins with two key ingredients: acetone and hydrogen cyanide. These chemicals are not household names, but they are the building blocks of methyl methacrylate (MMA), the monomer that forms the backbone of acrylic, scientifically known as polymethyl methacrylate (PMMA). Acetone, a common solvent, is derived from petroleum, while hydrogen cyanide is typically produced as a byproduct of other industrial processes. These raw materials undergo a carefully controlled reaction to produce MMA, a colorless liquid with a sharp, distinctive odor.
The production of MMA is a critical first step, and manufacturers must ensure its purity. Impurities at this stage can compromise the clarity and strength of the final acrylic product. To achieve this, the MMA is distilled and refined, resulting in a high-quality monomer ready for polymerization—the process that transforms it into a solid plastic.
Polymerization: Turning Liquid into Solid
Polymerization is where the magic happens. MMA is combined with a catalyst, typically an organic peroxide, to initiate a chemical reaction that links the individual monomer molecules into long chains, forming PMMA. This process can take one of two main forms: bulk polymerization or suspension polymerization.
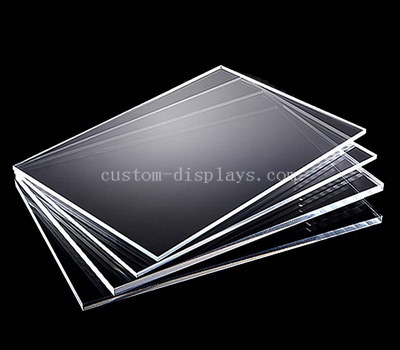
In bulk polymerization, the MMA is heated and cooled in molds or between glass sheets to create solid acrylic sheets directly. This method is commonly used to produce continuous sheets or slabs of acrylic, prized for their optical clarity and smooth surfaces. Suspension polymerization, on the other hand, involves dispersing MMA in water with a suspending agent and polymerizing it into tiny beads or granules. These beads can later be melted and reshaped into various forms, offering flexibility for manufacturers.
The choice of method depends on the intended end product. Sheets require the precision of bulk polymerization, while beads are ideal for injection molding or extrusion processes. Regardless of the approach, temperature, pressure, and reaction time must be meticulously controlled to ensure uniformity and quality.
Shaping the Product: Casting, Extrusion, and Molding
Once PMMA is formed, it’s time to shape it into usable products. Acrylic can be cast, extruded, or molded, depending on the desired outcome.
Casting is the go-to method for producing high-quality acrylic sheets. In this process, liquid PMMA is poured into molds—often between two glass panes—and allowed to solidify. The result is a thick, durable sheet with exceptional clarity, ideal for applications like windows, aquariums, or signage. Cast acrylic is known for its superior surface finish and resistance to scratches, making it a premium choice.
Extrusion, by contrast, is a faster, more cost-effective method suited for producing thinner sheets or continuous lengths of acrylic. Here, PMMA beads are melted and forced through a die to create uniform shapes, such as tubes, rods, or thin films. Extruded acrylic may lack the optical perfection of cast acrylic, but its affordability and versatility make it popular for everyday uses like lighting fixtures and packaging.
For more complex shapes—like car taillights, medical devices, or decorative objects—injection molding comes into play. PMMA beads are heated until molten and injected into precision molds under high pressure. Once cooled, the acrylic takes on intricate details with remarkable accuracy, showcasing its adaptability.
Finishing Touches: Polishing and Quality Control
Raw acrylic, whether cast, extruded, or molded, often requires finishing to achieve its signature look and performance. Edges may be rough or surfaces slightly imperfect after initial shaping, so manufacturers employ techniques like sanding, buffing, and flame polishing to smooth them out. Flame polishing, for instance, uses a controlled heat source to briefly melt the surface, leaving it glossy and clear—a hallmark of high-quality acrylic.
Color can also be introduced during manufacturing. While acrylic is naturally transparent, pigments or dyes can be added to the MMA before polymerization or mixed into molten PMMA during extrusion or molding. This allows for a spectrum of hues, from vibrant reds to subtle tints, expanding its aesthetic possibilities.
Quality control is the final, crucial step. Each piece is inspected for defects like bubbles, scratches, or inconsistencies in thickness. Advanced tools, such as lasers and optical scanners, ensure that the acrylic meets strict standards for clarity, strength, and dimensional accuracy. Only then is it deemed ready for the market.
Applications and Impact
The end result of this intricate process is a material that’s lightweight yet strong, transparent yet customizable, and resistant to weathering and UV light. Acrylic sheets grace skyscraper windows, while molded components enhance automotive designs. Artists sculpt with it, retailers display products on it, and homeowners enjoy it in furniture and fixtures. Its recyclability—through melting and reforming—also adds an eco-friendly dimension to its appeal.
Conclusion
From the humble beginnings of acetone and hydrogen cyanide to the gleaming sheets and shapes that define modern design, acrylic manufacturing is a testament to human ingenuity. It’s a process that balances chemistry and craftsmanship, transforming raw materials into a material that’s both practical and beautiful. Next time you admire a crystal-clear acrylic panel or a brightly colored molded object, consider the journey it took to reach you—a journey of precision, innovation, and endless possibility.